Porosity in Welding: Identifying Common Issues and Implementing Finest Practices for Prevention
Porosity in welding is a prevalent concern that usually goes unnoticed till it triggers considerable troubles with the honesty of welds. In this discussion, we will discover the crucial factors adding to porosity development, examine its detrimental effects on weld performance, and discuss the finest practices that can be adopted to minimize porosity incident in welding processes.
Common Reasons For Porosity
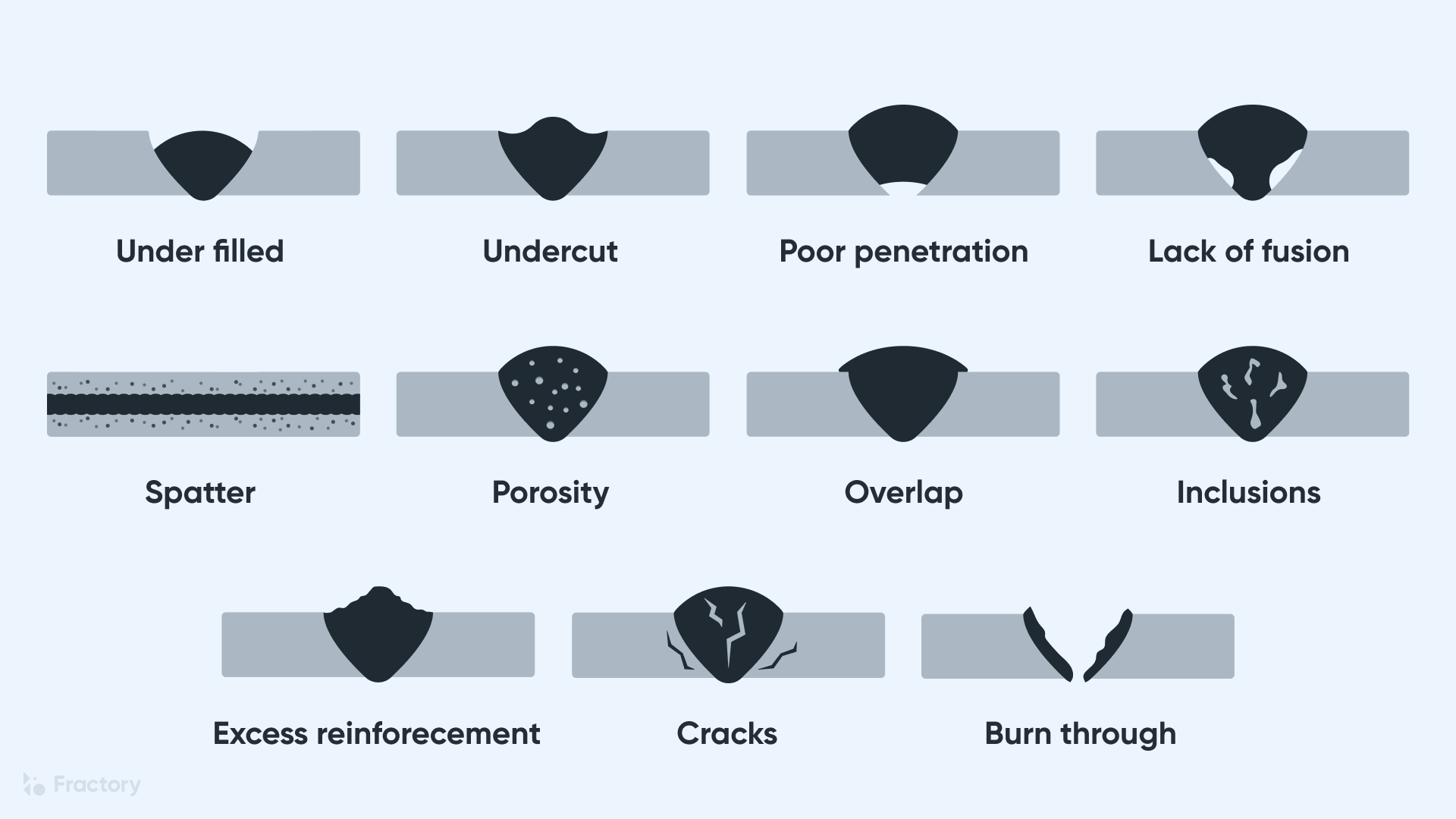
An additional frequent offender behind porosity is the existence of contaminants externally of the base steel, such as oil, grease, or rust. When these contaminants are not effectively eliminated prior to welding, they can evaporate and end up being trapped in the weld, triggering defects. In addition, using filthy or wet filler products can present pollutants right into the weld, contributing to porosity concerns. To reduce these typical reasons for porosity, detailed cleaning of base steels, correct shielding gas choice, and adherence to ideal welding parameters are important methods in achieving top quality, porosity-free welds.
Impact of Porosity on Weld High Quality

The existence of porosity in welding can considerably compromise the structural stability and mechanical buildings of welded joints. Porosity develops spaces within the weld steel, weakening its general toughness and load-bearing capability. These spaces function as stress and anxiety focus factors, making the weld a lot more vulnerable to splitting and failing under used loads. Furthermore, porosity can lower the weld's resistance to corrosion and other environmental factors, better reducing its long life and performance.
Welds with high porosity levels tend to exhibit lower influence toughness and reduced ability to warp plastically prior to fracturing. Porosity can impede the weld's capacity to successfully send forces, leading to premature weld failing and potential safety and security threats in vital frameworks.
Finest Practices for Porosity Prevention
To enhance the architectural stability and high quality of bonded joints, what specific procedures can be implemented to reduce the incident of porosity throughout the welding procedure? Porosity avoidance in welding is essential to guarantee the stability and stamina of the last weld. One efficient method appertains cleansing of the base steel, eliminating any type of impurities such as rust, oil, paint, or wetness that can lead to gas entrapment. Making certain that the welding tools is in good problem, with tidy consumables and appropriate gas flow rates, can also considerably lower porosity. In addition, keeping a secure arc and regulating the welding criteria, such as voltage, existing, and travel rate, assists create a regular weld pool that minimizes the danger of gas entrapment. Making use of the appropriate welding technique for the specific product being welded, such as adjusting the welding angle and weapon placement, can even more prevent porosity. Regular examination of welds and immediate remediation of any problems recognized throughout the welding procedure are essential practices to avoid porosity and create high-grade welds.
Relevance of Correct Welding Strategies
Implementing appropriate welding methods is paramount in making sure the architectural integrity and quality of bonded joints, building on the my company foundation of effective porosity avoidance measures. Welding methods directly impact the total toughness and longevity of the bonded structure. One crucial aspect of correct welding methods is maintaining the proper warmth input. Too much heat can bring about enhanced porosity because of the entrapment of gases in the weld pool. Conversely, inadequate heat may result in incomplete fusion, producing prospective weak factors in the joint. Additionally, using the ideal welding criteria, such as voltage, existing, and travel speed, is vital for accomplishing sound welds this hyperlink with very little porosity.
Additionally, the selection of welding procedure, whether it be MIG, TIG, or stick welding, should line up with the specific needs of the task to make sure optimum results. Appropriate cleansing and preparation of the base metal, along with picking the right filler material, are likewise essential elements of proficient welding methods. By sticking to these ideal practices, welders can reduce the danger of porosity development and produce premium, structurally audio welds.
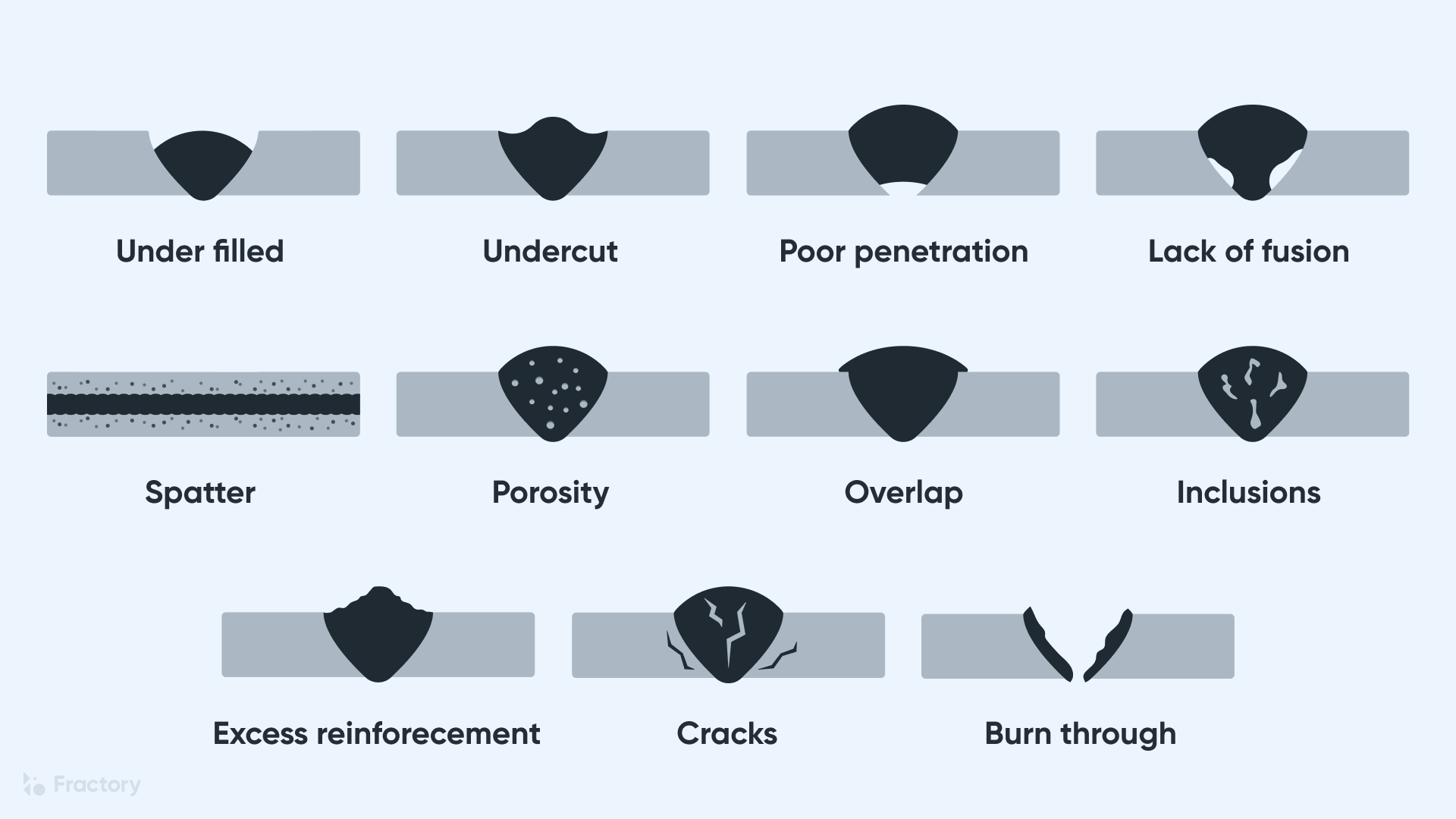
Examining and Quality Control Procedures
Checking treatments are necessary to identify and protect against porosity in welding, ensuring the toughness and durability of the final item. Non-destructive screening approaches such as ultrasonic screening, radiographic screening, and visual examination are commonly utilized to recognize possible flaws like porosity.
Post-weld assessments, on the other hand, examine the last weld for any flaws, consisting of porosity, and confirm that it satisfies defined standards. Carrying out a comprehensive high quality control strategy that consists of comprehensive testing treatments and inspections is vital to lowering porosity issues and guaranteeing the general top quality of bonded joints.
Conclusion
To conclude, porosity in welding can be a typical concern that influences the quality of welds. By identifying the typical sources of porosity and carrying out ideal techniques for prevention, such as proper welding techniques and testing steps, welders can make sure top quality and reliable welds. It is vital to prioritize prevention techniques to reduce the occurrence of porosity and keep pop over to these guys the honesty of welded structures.