Porosity in Welding: Identifying Common Issues and Implementing Ideal Practices for Prevention
Porosity in welding is a pervasive problem that frequently goes undetected up until it causes significant troubles with the integrity of welds. This common flaw can compromise the stamina and resilience of bonded frameworks, posing security dangers and resulting in costly rework. By comprehending the source of porosity and executing efficient avoidance strategies, welders can substantially enhance the high quality and dependability of their welds. In this discussion, we will certainly explore the key elements adding to porosity formation, examine its detrimental effects on weld efficiency, and review the very best techniques that can be taken on to minimize porosity incident in welding procedures.
Common Sources Of Porosity

Using unclean or damp filler materials can present contaminations right into the weld, contributing to porosity problems. To minimize these common causes of porosity, complete cleansing of base steels, proper securing gas selection, and adherence to ideal welding specifications are crucial practices in achieving premium, porosity-free welds.
Influence of Porosity on Weld Top Quality

The existence of porosity in welding can considerably jeopardize the structural stability and mechanical buildings of welded joints. Porosity develops gaps within the weld steel, damaging its total stamina and load-bearing capability.
Welds with high porosity levels have a tendency to exhibit reduced effect strength and minimized capacity to warp plastically prior to fracturing. Porosity can hinder the weld's capacity to effectively transmit forces, leading to premature weld failure and potential security threats in vital frameworks.
Ideal Practices for Porosity Avoidance
To enhance the architectural integrity and high quality of bonded joints, what specific actions can be implemented to reduce the occurrence of porosity during the welding process? Using the proper welding method for the specific material being welded, such as changing the welding angle and gun position, can even more protect against porosity. Routine inspection of welds and instant remediation of any type of issues recognized throughout the welding procedure are crucial practices to protect against porosity and generate top notch welds.
Value of Appropriate Welding Methods
Implementing appropriate welding strategies is critical in making certain the structural stability and quality of bonded joints, developing upon the foundation of reliable porosity avoidance steps. Welding techniques straight affect the overall toughness and toughness of the welded framework. One crucial aspect of correct welding methods is maintaining the proper warm input. Excessive warmth can cause increased porosity as a result of the entrapment of company website gases in the weld pool. Conversely, inadequate heat might result in insufficient combination, developing possible powerlessness in the joint. Additionally, utilizing the proper welding criteria, such as voltage, current, and take a trip speed, is vital for achieving audio welds with minimal porosity.
Moreover, the option of welding process, whether it be MIG, TIG, or stick welding, should align with the details needs of the job to make sure optimum results. Correct cleansing and preparation of the base metal, along with picking the right filler material, are likewise necessary parts of proficient welding techniques. By adhering to these finest methods, welders can decrease the threat of porosity development and generate high-quality, structurally audio welds.
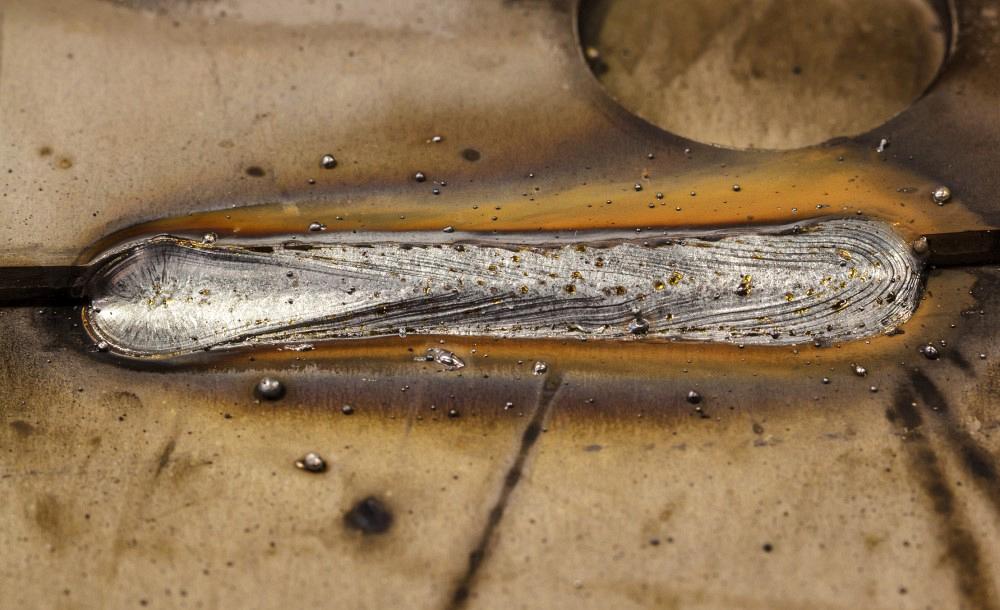
Evaluating and Quality Control Measures
Examining treatments are essential to find and prevent porosity in welding, making certain the strength and longevity of the final item. Non-destructive testing techniques such as ultrasonic testing, radiographic testing, and aesthetic examination are frequently utilized to determine potential defects like porosity.
Post-weld examinations, on the other hand, examine the last weld for any problems, consisting of porosity, and confirm that it satisfies defined criteria. Executing a thorough quality control plan that consists of check that detailed testing procedures and assessments is paramount to decreasing porosity concerns and making certain the overall high quality of bonded joints.
Verdict
In conclusion, porosity in welding can be a common problem that impacts the quality of welds. By recognizing the common sources of porosity and carrying out ideal techniques for prevention, such as proper welding techniques and testing procedures, welders can make sure premium quality and reliable view website welds. It is necessary to prioritize prevention techniques to reduce the incident of porosity and preserve the stability of welded structures.